Fasteners and Machining: Enhancing the Manufacturing Process
Fasteners and Machining: Enhancing the Manufacturing Process
Blog Article
Revealing the Details of Fasteners and Machining Procedures for Optimal Performance
In the world of design and manufacturing, the option of fasteners and the ins and outs of machining procedures play a critical function in identifying the best efficiency and toughness of a product. From the apparently simple job of picking the ideal kind of bolt to the complex precision machining techniques used, every step in this process needs precise interest to detail. As we start this exploration right into the world of fasteners and machining, we will certainly reveal the subtle yet important aspects that can dramatically affect the efficiency and top quality of the final item, dropping light on the commonly neglected elements that can make all the distinction in achieving ideal performance.
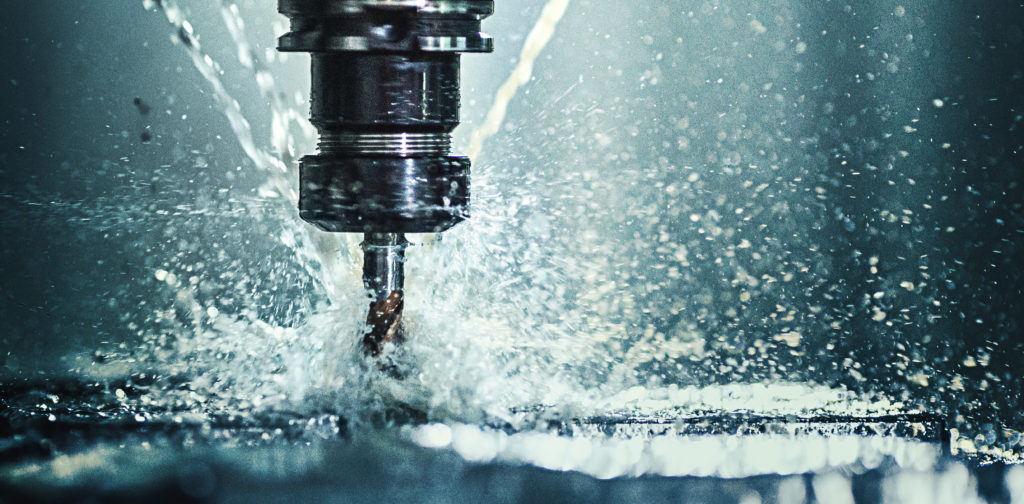
Significance of Correct Bolt Selection
Choosing the proper fasteners is crucial in guaranteeing the structural integrity and long life of any kind of mechanical setting up. Bolts play a basic function in holding components with each other firmly, with the ideal selection adding dramatically to the overall performance and integrity of the setting up. When selecting fasteners, factors such as product compatibility, ecological conditions, load-bearing capacity, and simplicity of setup have to be very carefully taken into consideration to ensure optimum efficiency.
Incorrect fastener selection can lead to a series of problems, consisting of helping to loosen, deterioration, and even architectural failing. Making use of bolts that are not matched to the specific requirements of the assembly can endanger its performance and pose safety and security dangers. For that reason, designers and developers should diligently review the application requires and pick bolts that fulfill or go beyond the essential standards and requirements.
Furthermore, the right fastener selection procedure includes analyzing the joint layout, anticipated lots, vibration degrees, and potential thermal development or contraction to guarantee that the picked fasteners can withstand the operating conditions properly. By prioritizing proper fastener option, suppliers can boost the top quality, toughness, and efficiency of their mechanical settings up.
Kinds and Characteristics of Fasteners
A necessary aspect of mechanical settings up depends on understanding the varied types and distinct characteristics of bolts utilized in different commercial applications. Bolts are important elements that hold structures together, guaranteeing security and functionality. There is a vast array of fasteners available, each developed for specific purposes based on the application demands. Common sorts of fasteners include screws, screws, nuts, washing machines, pins, and rivets.
Screws are threaded fasteners that are frequently used to sign up with two or even more elements with each other. Screws resemble screws however are generally used with a nut to create a safe joint. Nuts are internally threaded bolts that mate with screws to hold parts together. Washing machines are slim plates that distribute the tons of a fastener, protecting against damage to the product being attached. Rivets are irreversible bolts that are hammered or pushed into area. Pins are utilized for positioning or to safeguard parts briefly.
Understanding the features of each kind of fastener is necessary for selecting the best one for a particular application, guaranteeing optimum efficiency and integrity of the mechanical setting up. Fasteners and Machining.
Precision Machining Techniques for Performance
The elaborate design requirements of various bolts demand using precision machining techniques for optimal effectiveness in manufacturing processes. One of the main methods used in accuracy machining is Computer system Numerical read review Control (CNC) machining, which enables high levels of accuracy and repeatability in the production of bolts.
Along with CNC machining, other accuracy methods such as grinding, milling, and transforming are generally used to accomplish Recommended Reading the tight tolerances required for fasteners. These methods permit suppliers to create bolts with smooth surface areas, specific measurements, and high structural integrity. By utilizing accuracy machining strategies, suppliers can enhance the high quality of fasteners, minimize material waste, and improve total production performance. The usage of sophisticated machining processes aids make sure that fasteners meet market standards and consumer expectations for efficiency and dependability.

Variables Influencing Machining Process Performance
Numerous variables play a considerable duty in identifying the efficiency of machining procedures in the manufacturing of fasteners. The very first essential factor is the choice of reducing tools. Selecting the ideal tools based on the product being machined, wanted coating, and reducing speeds can significantly impact the effectiveness and high quality of the machining process. Furthermore, the reducing criteria such as reducing rate, feed price, and deepness of cut are necessary variables that affect efficiency. Fasteners and Machining. Maximizing these parameters based on the specific requirements of the fastener being generated is crucial to accomplishing accurate and economical machining.
Device strength and stability likewise play a critical function in identifying machining procedure efficiency. A well-informed driver can make real-time modifications, troubleshoot concerns efficiently, and guarantee that the machining my response process runs efficiently, ultimately affecting the final quality of the fastener.
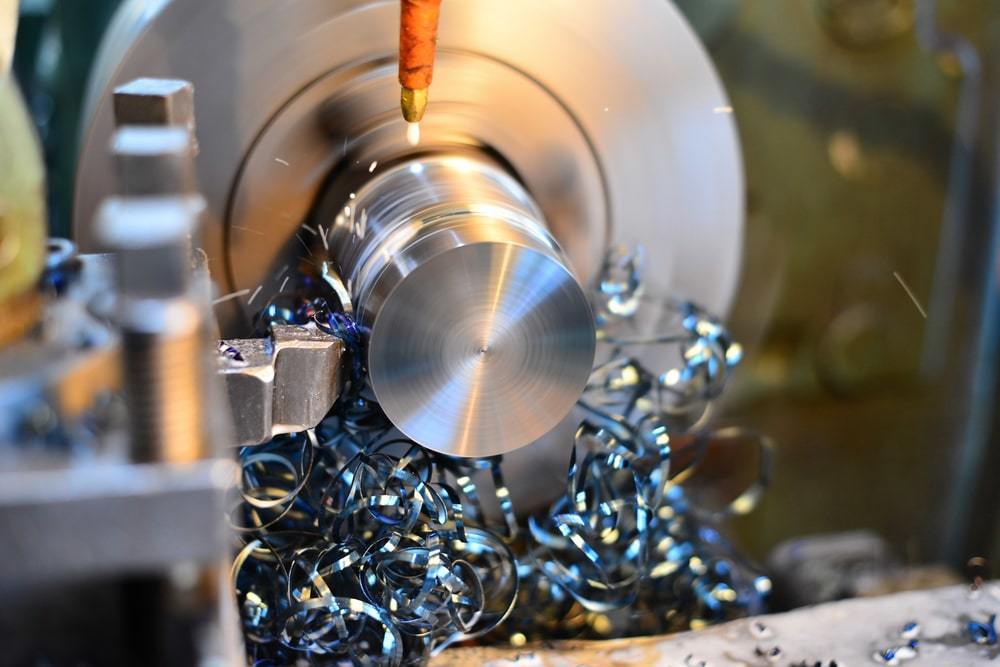
Quality Assurance Measures in Manufacturing
Aspects affecting machining procedure performance, such as reducing tool option and machine security, straight impact the application of top quality control procedures in production. Routine upkeep of machining tools is also vital to copyright quality control. By adhering to rigorous high quality control procedures, suppliers can improve customer fulfillment, construct an online reputation for dependability, and ultimately attain optimum efficiency in their machining procedures.
Verdict
To conclude, picking the appropriate bolts and making use of accuracy machining techniques are crucial for optimum efficiency in producing processes. Understanding the kinds and characteristics of fasteners, together with elements affecting machining process performance, can lead to improved effectiveness and high quality control procedures. By focusing on these details, makers can attain greater degrees of performance and integrity in their products.
In the realm of engineering and manufacturing, the choice of bolts and the complexities of machining procedures play an essential duty in establishing the utmost performance and toughness of an item (Fasteners and Machining). One of the main strategies utilized in precision machining is Computer Numerical Control (CNC) machining, which enables high levels of accuracy and repeatability in the production of fasteners. The usage of innovative machining procedures helps guarantee that fasteners satisfy sector criteria and client expectations for efficiency and dependability
In final thought, selecting the best bolts and making use of accuracy machining strategies are vital for ideal efficiency in manufacturing processes. Recognizing the types and characteristics of fasteners, along with variables affecting machining process efficiency, can lead to improved efficiency and quality control actions.
Report this page